Bei Schrittmotoren und Schrittmotor-Steuerungen gibt es verschiedene Sichtweisen auf den Phasenstrom. Bei der Auswahl der Komponenten ist es hilfreich, diese Unterschiede zu kennen und entsprechend zu berücksichtigen. Mit diesem Beitrag möchte ich diese unterschiedlichen Betrachtungsweisen verständlich machen.
Phasenstrom bei Schrittmotoren
Der bei Schrittmotoren angegebene Phasenstrom (Motornennstrom) bezieht sich immer auf eine Vollschritt-Position, in der beide Phasen mit dem gleichen Strom durchflossen sind. Diese Betrachtung ist einleuchtend, wenn man sich vor Augen führt, dass der Vollschritt-Betrieb lange Zeit die Standard-Betriebsart war. Auch beim Aufkommen von Halbschritt-fähigen Steuerungen wurde zunächst der Wicklungsstrom nicht variiert, sondern in den Halbschritt-Positionen lediglich eine der Wicklungen abgeschaltet. Erst mit dem Aufkommen von 1/4-Schritt fähigen Treiber-ICs fing man an, in den Halbschritt-Positionen den Motorstrom anzuheben, siehe unten.
Betrachtet man die elektrischen Verluste im Motor (bei stehendem Rotor), ergeben sich diese zu
Pel = n * Imotor2 * R ; mit n = Anzahl der Wicklungen, Imotor = Inennstrom, R = Wicklungswiderstand
Der Nennstrom wird vom Hersteller so bemessen, dass der Schrittmotor im Dauerbetrieb thermisch nicht überlastet wird. Üblicherweise wird dabei auch eine Montage mit definierten Bedingungen (erforderliche Auflagefläche für den Motorflansch) vorausgesetzt. Anmerkung: Bei Montage des Motors über einzelne Stehbolzen ohne flächige Auflage kann die Wärme nicht an die umliegende Mechanik abgegeben werden. Der Motorstrom muss in solchen Anwendungen entsprechend reduziert werden.
Das von beiden Phasen erzeugte Motormoment ergibt sich durch die vektorielle Addition der Momente aus den einzelnen Phasen. Da diese bei einem 2-phasigen Motor elektrisch 90° zueinander stehen, ergibt sich das resultierende Moment wie folgt:
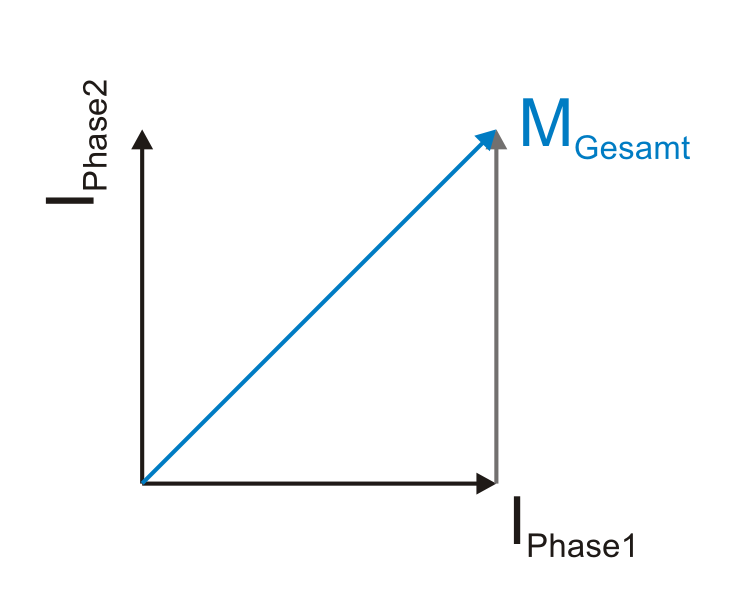
Anpassung des Wicklungsstroms in der Schrittmotor-Steuerung
Um die Auflösung des Motors zu erhöhen, wurde der Halbschritt-Betrieb eingeführt. Hierbei wird in den zusätzlichen Halbschritt-Positionen jeweils eine der beiden Phasen abgeschaltet. Das Motormoment ist direkt proportional zum Motorstrom. Es ergibt sich also ein um den Faktor 1/Wurzel(2) = ~0,707-fach geringeres Moment. Um eine Welligkeit des Drehmomentes zu vermeiden empfiehlt es sich, den Phasenstrom entsprechend um den Faktor Wurzel(2) anzuheben. Das ist zulässig ohne den Motor thermisch zu überlasten, wie man leicht nachrechnen kann. Obige Formel gilt weiterhin, nun allerdings mit n = 1 und Imotor = Wurzel(2) * Inenn.

Diese Art des modifizierten Halbschritt-Betriebs wird in älteren Application-Notes von ST als „Halfstep with shaping“ bezeichnet, und wurde z.B. bei der ersten Schrittmotor-Steuerung von mir, der 3D-Step, schon 2001 umgesetzt.
Übergang zum Mikroschritt
Fügt man weitere Zwischenschritte für die beiden Phasenströme ein, wird der Motor im sogenannten Mikroschritt angesteuert. Üblich sind Unterteilungen eines Vollschritts in 4 („Viertelschritt) bis 256 Schritte (1/256 Mikroschritt). Eine detailiertere Erklärung findet sich bei Prof. Jones, einschließlich einer Anekdote über die Erfindung der Mikroschritt-Ansteuerung 1974. Für die Ströme in den Wicklungen ergeben sich zwei Sinus-förmige Verläufe mit einer Phasenverschiebung von 90°. Der Verlauf des Drehmoments ist (nahezu) konstant, wenn man das Rastmoment des Motors außeracht lässt.

Das Rastmoment eines Schrittmotors liegt üblicherweise bei etwa 5% des Nennmoments und kann in der Praxis durchaus zu hörbaren Laufgeräuschen führen. Wenn die verwendete Motorsteuerung keine Kompensationsmöglichkeit bietet, wird die tatsächlich erreichbare Mikroschritt-Auflösung limitiert. Realisiert ist eine solche Kompensation z.B. in der DS10-Serie von LAM.
Strom ist nicht gleich Strom
Wie in den vorherigen Abschnitten gezeigt wurde, haben Hersteller von Schrittmotoren und Schrittmotor-Steuerungen unterschiedliche Sichten auf den Motorstrom. Beim Motor ist der Motornennstrom die entscheidende Kenngröße. In der Steuerung wird dieser Strom in der Halbschritt-Position erreicht und entspricht etwa 70,7% des eingestellten Motorstroms.
Um Schrittmotor-Steuerungen gut vermarkten zu können, hat es sich mit dem Aufkommen von Mikroschritt Steuerungen schnell eingebürgert, den höheren Spitzenwert des sinusförmigen Wicklungsstroms anzugeben. Dieser ist aber – wie oben hergeleitet – um den Faktor Wurzel(2) = ~1,412-fach größer als der Nennstrom des Motors. Um einen Motor mit 2,0A Wicklungsstrom mit seinem Nennmoment betreiben zu können, ist also ein Treiber mit einem Ausgangsstrom von 2,8A erforderlich. Bei den Produkten von mechapro geben wir in der Regel beide Werte an, Effektivwert (=Motornennstrom) und Spitzenwert (zur Vergleichbarkeit mit Wettbewerbs-Produkten).
Fazit
Bei Schrittmotor-Steuerungen wird oft nur der höhere Spitzenstrom angegeben. Um den Schrittmotor auch tatsächlich mit seinem nominalen Haltemoment und entsprechendem Drehmoment betreiben zu können, muss die Endstufe der Motorsteuerung rund 140% des Motornennstroms bereitstellen können. Und das je nach Anwendung nicht nur kurzzeitig, sondern im Dauerbetrieb. Bei der Auswahl einer Steuerung muss also ausreichend Reserve berücksichtigt werden, um den Schrittmotor optimal ausnutzen zu können.