In den letzten 10 Jahren sind die Preise bei Schrittmotoren deutlich unter Druck geraten, vor allem wegen der billigen Produkte aus China. Für den Anwender stellt sich die Frage, wie die Qualität der Motoren zu bewerten ist, da der Preis wie so oft nur bedingt einen Rückschluss auf die Qualität des Produkts zulässt. Im folgenden Beitrag möchte ich daher auf einige Eigenschaften von Schrittmotoren eingehen und aufzeigen, welche Unterschiede es im Detail gibt.
Blechpaket / Stator
Zur Vermeidung von Wirbelstromverlusten wird der Stator des Schrittmotors geblecht ausgeführt. Die Statorbleche sind mit einem Backlack beschichtet, der nach Aufbau des Blechpakets im Ofen verbacken wird, um mechanische Stabilität zu erreichen. Zusätzliche Stabilität erhält der Motor durch die Verschraubung, welche vom vorderen bis zum hinteren Lagerschild reicht. Die Lagerschilde werden aus Gußrohlingen hergestellt, bei denen lediglich die Funktionsflächen (Lagersitze, Montageflansch mit Zentrierbund) spanabhebend nachbearbeitet werden.
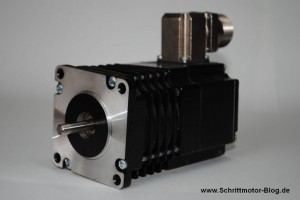
Wo rohe Kräfte sinnlos walten… Bei diesem 5-phasen Schrittmotor von Berger Lahr wurde das Statorgehäuse durch eine übermäßige Drehmoment-Belastung tordiert.
Insbesondere bei preiswerten Motoren werden die Bleche zusätzlich mit mehreren Nähten verschweißt, was an den Schweißnähten naheliegender weise für erhöhte Verluste sorgt. Bei inzwischen erhältlichen Motorlängen bis zu 112mm (bei Motoren mit 56mm Flanschmaß) ist diese Maßnahme kaum zu vermeiden. Bei Motoren mit lediglich 56mm Länge sollte sich die Stabilität des Motors allerdings auch auf anderem Wege erreichen lassen.
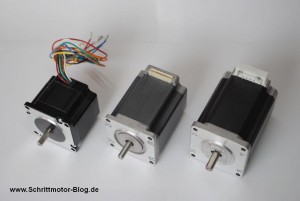
Von links nach rechts: Markenloser Chinamotor mit geschweißtem Blechpaket, Nidec Servo KH56QM2 mit gleichmäßiger, ungeschweißter Blechung und Sanyo Denki 103H7823 mit sichtbarem Lagenaufbau.
Wie groß der Einfluss der Statorverluste im Dauerbetrieb sein kann, zeigt die Firma Oriental Motor in einer Wärmebildaufnahme. Vergleichen wurde ein Standardmotor mit der relativ neuen Motorserie PKE, welche mit dünneren Statorblechen aufgebaut wird, um die Verluste weiter zu reduzieren.

Wärmebildaufnahme zum Einfluss der Stator-Blechstärke auf die Erwärmung und damit die Verluste im Motor. Nach 80 Minuten ergibt sich eine Differenz von 40°C am Motorgehäuse [Quelle: Oriental Motor].
Das es auch unter den Motoren „Made in China“ deutliche Qualitätsunterschiede gibt, ist noch auf andere Ursachen zurückzuführen. Einige Importeure betreiben vor Ort eigene Qualitätssicherung und erreichen so geringere Fertigungs- und Montagetoleranzen. Andere Hersteller beziehen nur die Einzelteile aus China, führen die Endmontage aber in Europa durch. Dies gilt z.B. für die Schrittmotoren der italienischen Firma LAM. Abhängig von der Fertigungstiefe müssen diese Motoren aber trotzdem als „Made in China“ gekennzeichnet werden. Die großen japanischen Hersteller sind z.T. noch einen Schritt weiter, und fertigen große Serien schon nicht mehr in China, sondern in anderen asiatischen Ländern, in denen die Lohnkosten deutlich niedriger sind als in China. Durch die hohen Fertigungsstandards und die ISO-zertifizierte Qualitätssicherung ist hat das in der Regel jedoch keinen Einfluss auf die Qualität der Schrittmotoren.
Lager
Die für die Lagerung der Motorwelle verwendeten Kugellager sind die einzigen Verschleißteile bei Schrittmotoren. Insbesondere bei hohen radialen und axialen Kräften auf die Welle (z.B. bei Zahnriemen-Antrieben) haben sie wesentlichen Einfluss auf die Lebensdauer des Motors. Die Lagergröße ist bei Motoren mit Normflansch („Nema“-Baugrößen) durch die Geometrie des Motorflansches vorgegeben. Unterschiede finden sich dagegen bei den verwendeten Lagern selbst (hochwertige Markenprodukte oder preiswerte China-Ware) und bei den Fertigungstoleranzen im Lagerschild und an der Motorwelle. Diese Faktoren können nur durch Öffnen des Motors bzw. mehrerer Motoren geprüft werden, womit der Motor in der Regel unbrauchbar wird. Fertigungs- und Wicklungstoleranzen beeinflussen außerdem die mögliche Streuung in der Serienfertigung sowie Rastmoment und Positionsgenauigkeit im Mikroschritt, und damit das Geräusch und Resonanzverhalten der Schrittmotoren.
Motorwelle
Neben den Fertigungstoleranzen ist für den Anwender vor allem die äußere Ausführung des bzw. der Wellenenden von Interesse. Hierzu zählen Durchmesser, Länge und Querschnitt. War bei 56mm Flanschmaß („Nema23“) lange ein Wellendurchmesser von 6,35mm (1/4“) der Standard, werden viele Motoren mit höherem Drehmoment inzwischen mit 8,0mm Welle geliefert. Noch größer ist die Vielfalt bei Motoren mit 86mm Flansch („Nema34“), hier sind Wellendurchmesser 9,525mm, 12,0mm und 14,0mm gängig. Neben glatter Welle sind ein- oder zweiseitige Wellenabflachung (D-cut) und Wellen mit Passfedernut, sowie Motoren mit ein und zwei Wellenenden erhältlich. Je nach Hersteller gibt es unterschiedliche Standardausführungen, die bei Abnahme größerer Serien auch kundenspezifisch angepasst werden können. Das 2. Wellenende kann z.B. zur Montage von Handrädern, Dämpfern, Encodern oder Motorbremsen verwendet werden. Neben einer entsprechenden Wellenbearbeitung sind für die Montage z.T. auch passende Bohrungen oder Gewinde im hinteren Lagerschild erforderlich.

Von links nach rechts: China-Motor mit runder 6,35mm Welle, PKP268 mit 8,0mm Welle und einseitiger Abflachung, Sanyo Denki 103H7823 mit 8,0mm Welle und 2-facher Abflachung.
Litzen
Bei Motoren mit herausgeführten Leitungen gibt es deutliche Unterschiede bei den verwendeten Litzen. Gute Motoren sind mit sehr flexiblen Litzen ausgestattet, die sich durch einen feindrähtigen Aufbau und dünne, flexible Isoliermaterialien auszeichnen. Bei preiswerten Schrittmotoren sind die Litzen dagegen meist deutlich starrer, der innere Aufbau besteht aus weniger und dafür dickeren Drähten und die Isoliermaterialien sind steifer. Der Litzenaufdruck gibt Aufschluss über Querschnitt, Temperatur- und Spannungsfestigkeit sowie ggf. vorhandene Prüfsiegel (UL, CSA, VDE). Bei Ausführungen in IP54 wird ein mehradriges Kabel statt Einzeladern verwendet, und der Kabelausgang ist zusätzlich abgedichtet.

Links: China-Motor mit relativ starren Litzen, Kabeldurchführung durch Gumminippel. Rechts: PK266-E2.0B mit feindrähtigen Litzen, Kabeldurchführung mit Kantenschutz aus Kunststoff.
Kabelausgang / Stecker
Alternativ zum Herausführen von Anschlusslitzen gibt es verschiedene Varianten mit steckbaren Anschlüssen. Gängig sind Direkt-Steckverbindungen mit Steckern von JST, Molex oder Amphenol im Kunststoffgehäuse, mit oder ohne zusätzliche Abdeckung am Motorgehäuse. Vereinzelt sind auch Schrittmotoren mit integrierten Industriesteckern (M12) im Angebot, z.B. von Festo. Eine Zwischenlösung sind Motoren mit Klemmkasten am hinteren Lagerschild. Meist wird diese Variante gewählt, wenn die Schutzart IP65 erreicht werden muss. Der Anwender führt das Kabel über eine Kabelverschraubung („PG-Verschraubung“, heute meist mit metrischem Gewinde) in den Klemmkasten ein, wo die einzelnen Adern auf Schraubklemmen aufgelegt werden. Durch den Klemmkasten baut der Motor deutlich länger, die Abdichtung treibt außerdem die Kosten in die Höhe.

Verschiedene Ausführungen von Steckern bei Schrittmotoren. Von links nach rechts: Nidec Servo KH56QM2, Oriental Motor PKP268, Sanyo Denki 103H7823.
Kennlinie
Für die Auslegung des Antriebs spielen Drehzahl-Drehmoment Kennlinien eine wichtige Rolle. Sie geben Aufschluss darüber, welches Drehmoment der Motor bei verschiedenen Drehzahlen erreicht. Da die Kennlinien je nach Versorgungsspannung unterschiedlich ausfallen, ist es hilfreich, wenn Kennlinien für mehrere Spannungen zur Verfügung stehen. Zu sehr preiswerten Motoren aus unbekannter Fertigung bekommt man oft gar keine Kennlinien. Dann bleibt nur die Erprobung in der Applikation, wobei es sinnvoll ist, mit erhöhten Lasten zu arbeiten, um ausreichend Reserven zu berücksichtigen. Alle großen Hersteller stellen dagegen Kennlinien zu ihren Motoren zur Verfügung. Unter Umständen ist es sogar möglich, für spezielle Anwendungen (ungewöhnliche Versorgungsspannung, Betrieb mit geringerem Strom usw.), eine Kennlinie speziell nach Anforderungen des Anwenders aufzunehmen.
Verfügbarkeit
Die langfristige Verfügbarkeit von Ersatzteilen ist in kommerziellen Anwendungen ein gewichtiges Argument. Hier gibt es selbst bei den großen Herstellern unterschiedliche Philosophien und Produktlaufzeiten. Für einige Hersteller ist der europäische Markt relativ unbedeutend, entsprechend stiefmütterlich werden die Kunden behandelt, wenn es um Ersatzteile geht. In anderen Fällen bekommt man auch über 10 Jahre nach Auslaufen einer Serie problemlos einzelne Motoren als Ersatzteil. So lieferte z.B. Oriental Motor bis Frühjahr 2015 noch Motoren aus der 2-Phasen PH-Serie, welche Bereits in den 1990’er Jahren durch die bis heute verfügbare PK-Serie abgelöst wurde.
Fazit – Erforderliche Qualität hängt von der Anwendung ab
Wie man sieht, steckt der Teufel im Detail. Ob die vorgestellten Unterschiede relevant sind, hängt stark von der Applikation und den Ansprüchen an den Antrieb ab. Für private Anwendungen sind die meisten genannten Kriterien von untergeordneter Bedeutung, hier zählt für viele Anwender vor allem der Preis. In kommerziellen Applikationen sieht das ganz anders aus: Ist der Hersteller bzw. Lieferant flexibel genug, Wellenbearbeitung oder Anschlussleitung an die Kundenwünsche anzupassen, kann das in der Montage eine Menge Aufwand und damit Geld sparen. Falls dagegen der verwendete Schrittmotor nach 3 Jahren nicht mehr lieferbar ist, muss ein Ersatztyp qualifiziert werden. Soll z.B. das Endprodukt auf einmal in die USA exportiert werden, kommen Themen wie Prüfsiegel (UL) und Entflammbarkeitsklasse von Litzen und Steckern auf die Tagesordnung. Vor einer Entscheidung für einen Motor lohnt es sich also, verschiedene Typen zu vergleichen und dabei die genannten Kriterien im Blick zu behalten.